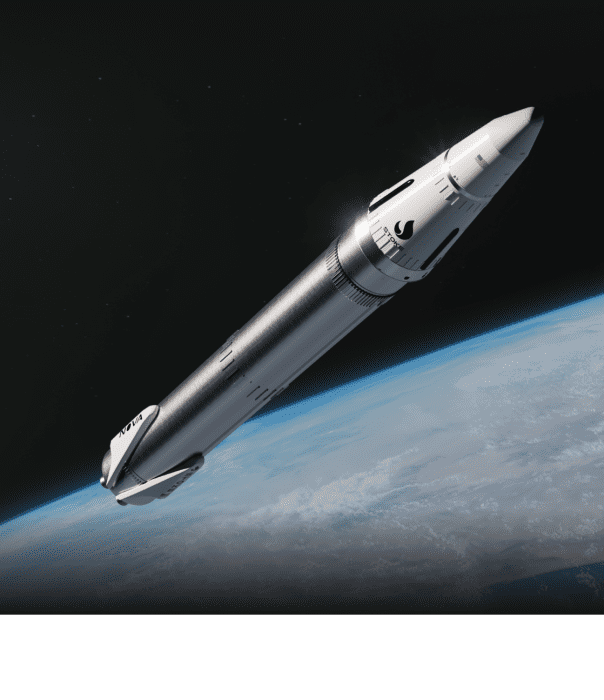
Nova: Engineered for full and rapid reuse
Nova’s fully reusable design changes the fundamentals of cost, availability, and reliability of launch. Full reusability means production costs are amortized across launches and flight frequency isn’t limited by production rates. And with 100% reusability, every mission uses flight-proven hardware.
The 100% reusable model also enables return shipments from space to Earth, unlocking new mission types and business opportunities. Not only does the rapidly reusable model make economic sense for today’s emerging market, it is the only approach to sustainably scaling the industry.
Refit, refuel, refly
Our reusable upper stage features a liquid, regeneratively cooled metallic reentry heat shield with an integrated modular liquid hydrogen/liquid oxygen (LH2/LOX) rocket engine. It’s robust, resilient to damage, and operates with passive failure modes.
Designed for minimal refurbishment between flights, our second stage unlocks rapid turnaround and offers:
- Direct access to GTO, TLI, and other high-energy orbits
- Unlimited engine restarts
- Return from orbit to launch site: precision, powered vertical landings
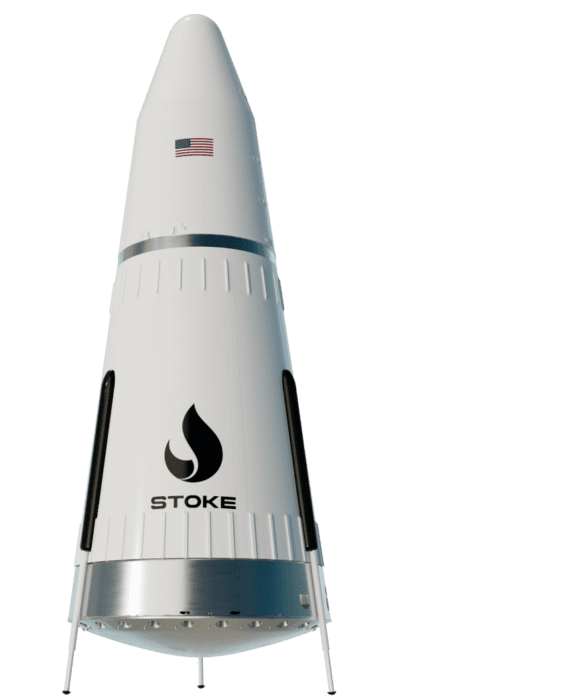
100% reusable payload fairing
180-degree by 360-degree deployment hemisphere
Dynamic space operations
Rendezvous, capture, and reposition assets with unprecedented in-space mobility
High thrust, high efficiency
High-Isp liquid hydrogen fuel and unlimited restarts create flexible mission architectures, including direct access to high-energy orbits
Unique nozzle geometry
Achieves world-class performance in a form that is shorter than traditional bell nozzles by a factor of 10, while also enabling deep-throttle operations, even in the atmosphere
Downmass capability
Debris/asset capture and return, and space cargo logistics. Axial loads during ascent, descent, and landing.
Reentry cross range capability
Enabled by a nontraditional conical shape, our vehicle employs meaningful cross range to steer the stage to a precise landing
Low ballistic coefficient
Vehicle uses aerodynamic drag to slow down from orbital velocities to less than 100 meters per second (224 mph) prior to restarting the engine for a soft vertical landing
Actively cooled metallic heat shield
The world’s most robust reentry heat shield enables reentry from high-energy orbits and landings on unprepared surfaces
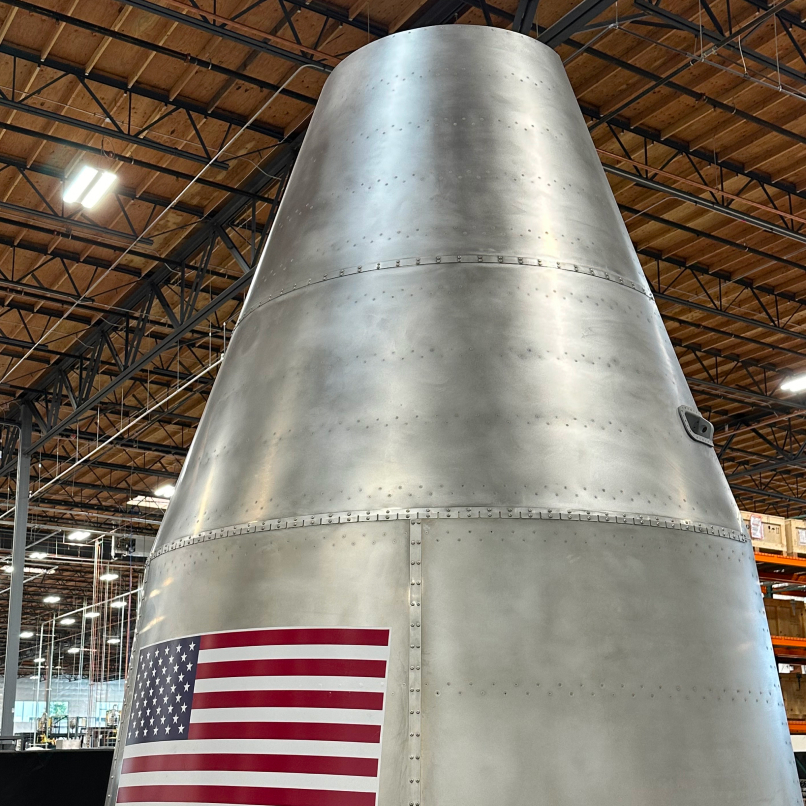
Fairing
Payload accommodations:
- 3,000 kg to LEO (100% reusable)
- 7,000 kg to LEO (max payload)
- 2,500 kg to GTO
- 1,250 kg to TLI
- 800 kg to C3 = 0
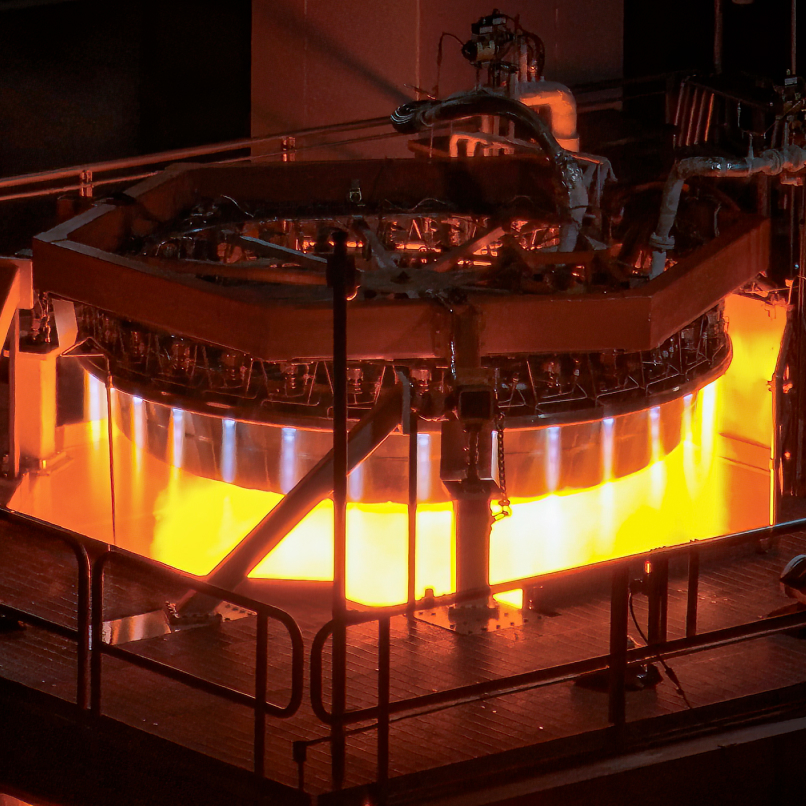
Stage 2
- Expander cycle with integrated heat shield
- Liquid hydrogen/liquid oxygen (LH2/LOX)
- 425+ s specific impulse (Isp)
- 25,000+ lbf thrust
LH2 fuel offers 30% higher efficiency and 5x better cooling than hydrocarbon fuels. With highest in-class performance and unlimited restarts, our stage 2 engine enables missions directly to high-energy orbits. The nozzle accommodates deep throttle operation even in the presence of atmospheric pressure and serves as an actively cooled metallic heat shield during atmospheric reentry.
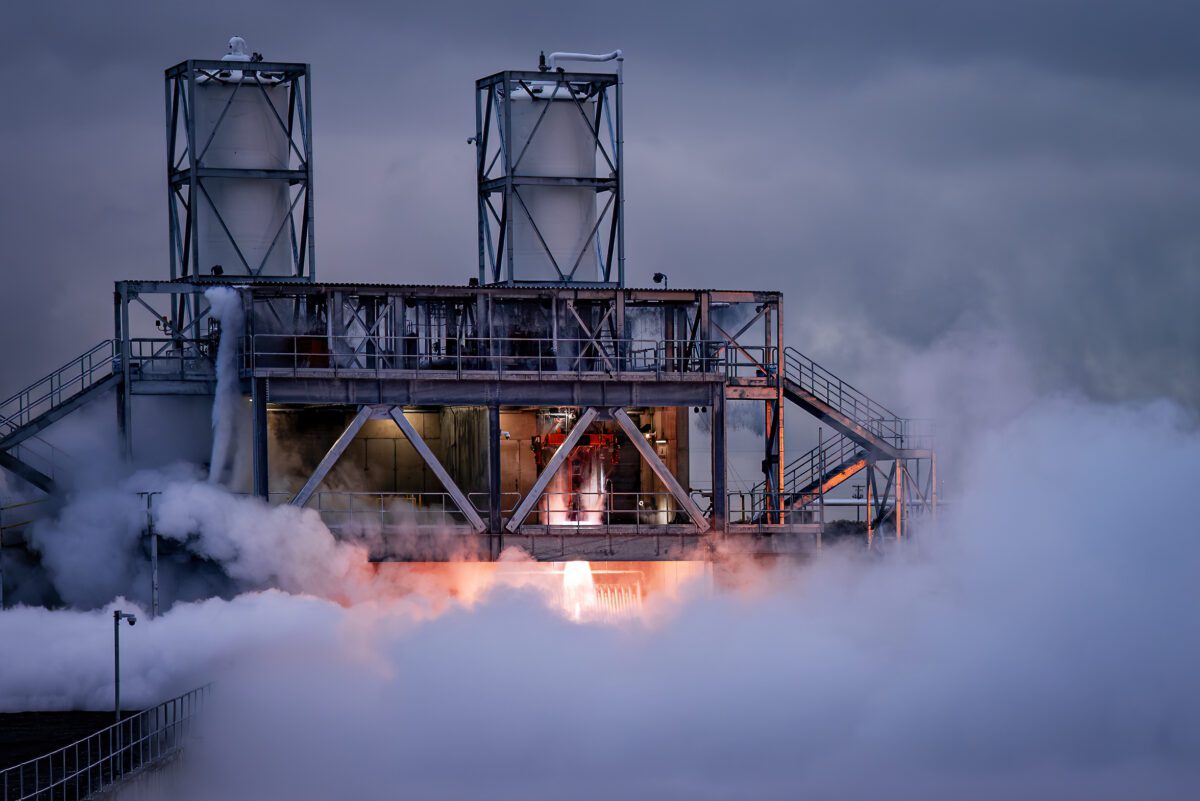
Stage 1
- Full-flow staged-combustion (FFSC)
- Liquified natural gas/liquid oxygen (LNG/LOX)
- 345 s specific impulse (Isp)
- 100,000+ lbf thrust
FFSC is the pinnacle of rocket engine cycles, providing high performance and high efficiency while stressing the engine less than other, simpler engine cycles. FFSC has the highest ceiling for performance, efficiency, long life, and rapid reusability.
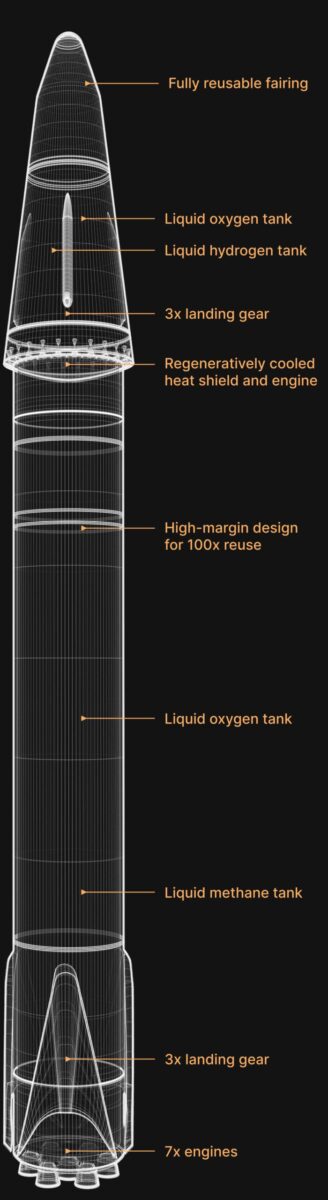
Rapid reusability requires design from the ground up.
The world’s first actively cooled heat shield reduces turnaround time — from months to hours.
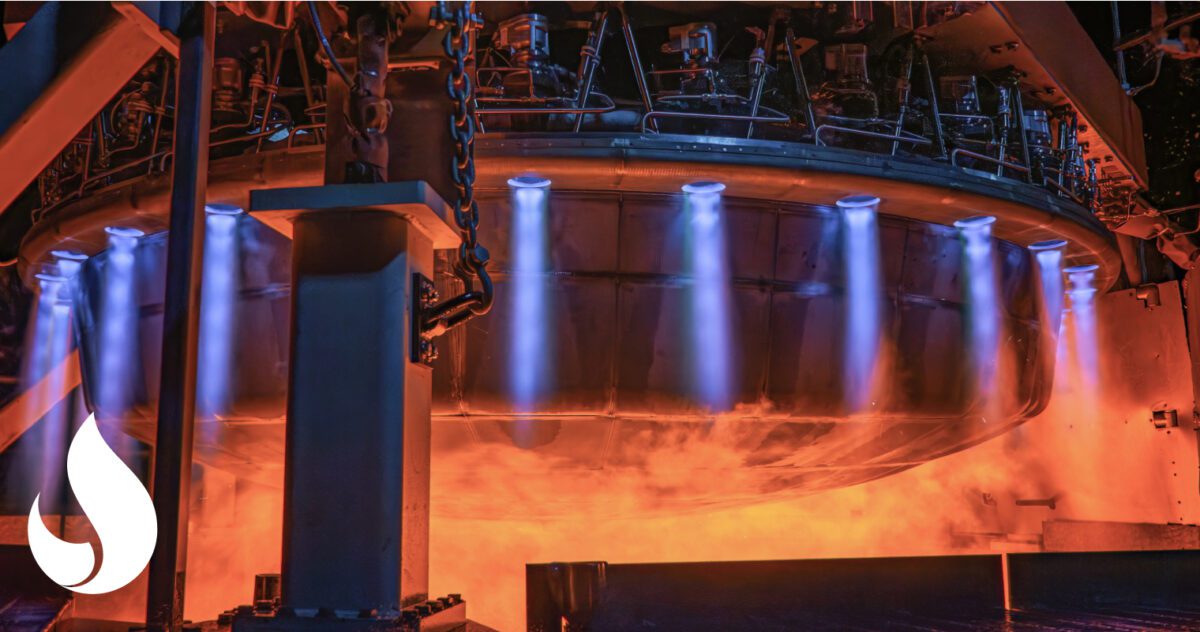
Stoke: cooled metallic heat shield
- Conventional materials
- Ductile materials
- Minimal maintenance
- Passive failure modes
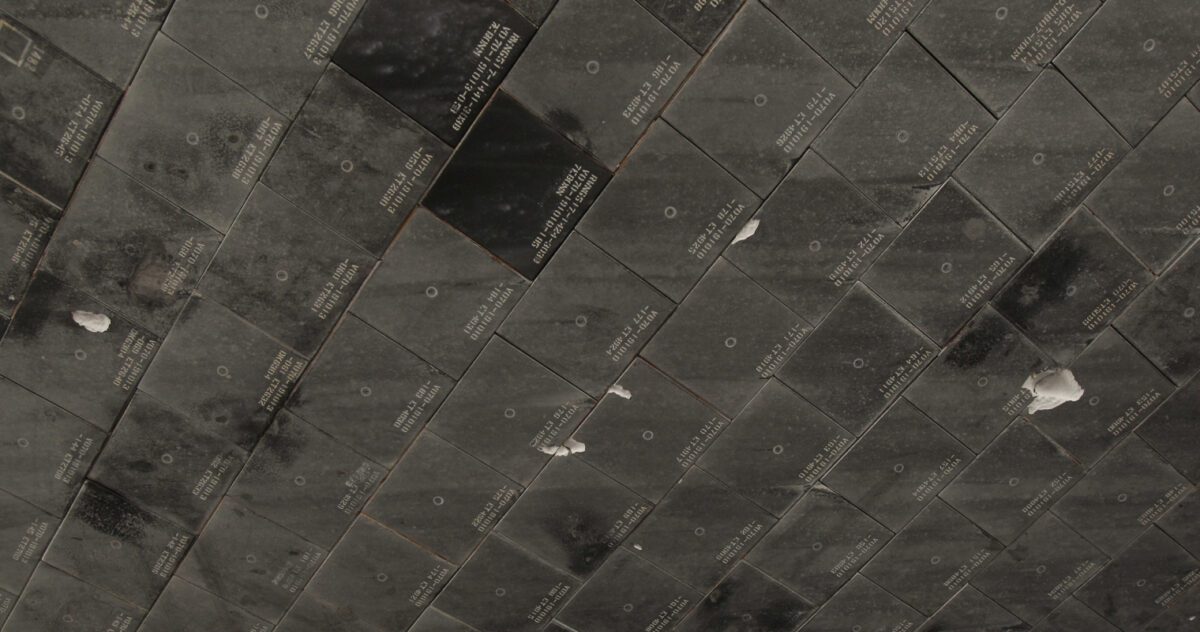
Competitors: ceramic tiles
- Expensive
- Brittle materials
- Constant maintenance
- Catastrophic failure modes
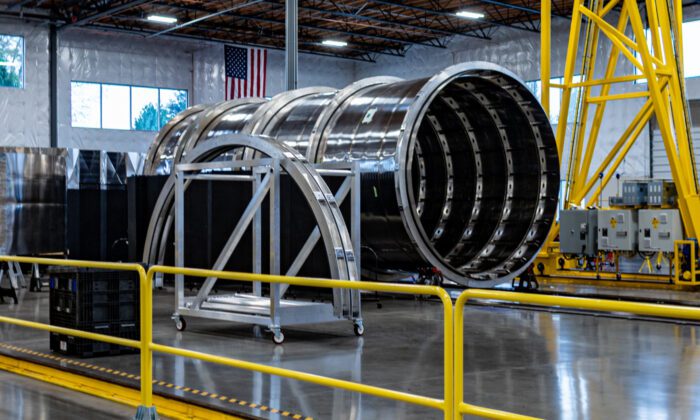
Manufacturing & testing
Our dynamic approach to design, testing, and production enables us to deliver high-quality, efficient, and fully reusable rockets at an unmatched pace.
We build in long life and rapid reusability from the start, using steel rather than carbon composite to give Nova’s tanks exceptional thermal properties, strength, and ductility. Steel tanks are better able to endure the multiple cycles of pressurization, high and low temperature cycles, and mechanical stresses of rapid reusability.
Located just a three-hour drive from our vertically integrated design, development, and manufacturing facility, our private test facility enables us to test, learn, and iterate faster than any other rocket company.