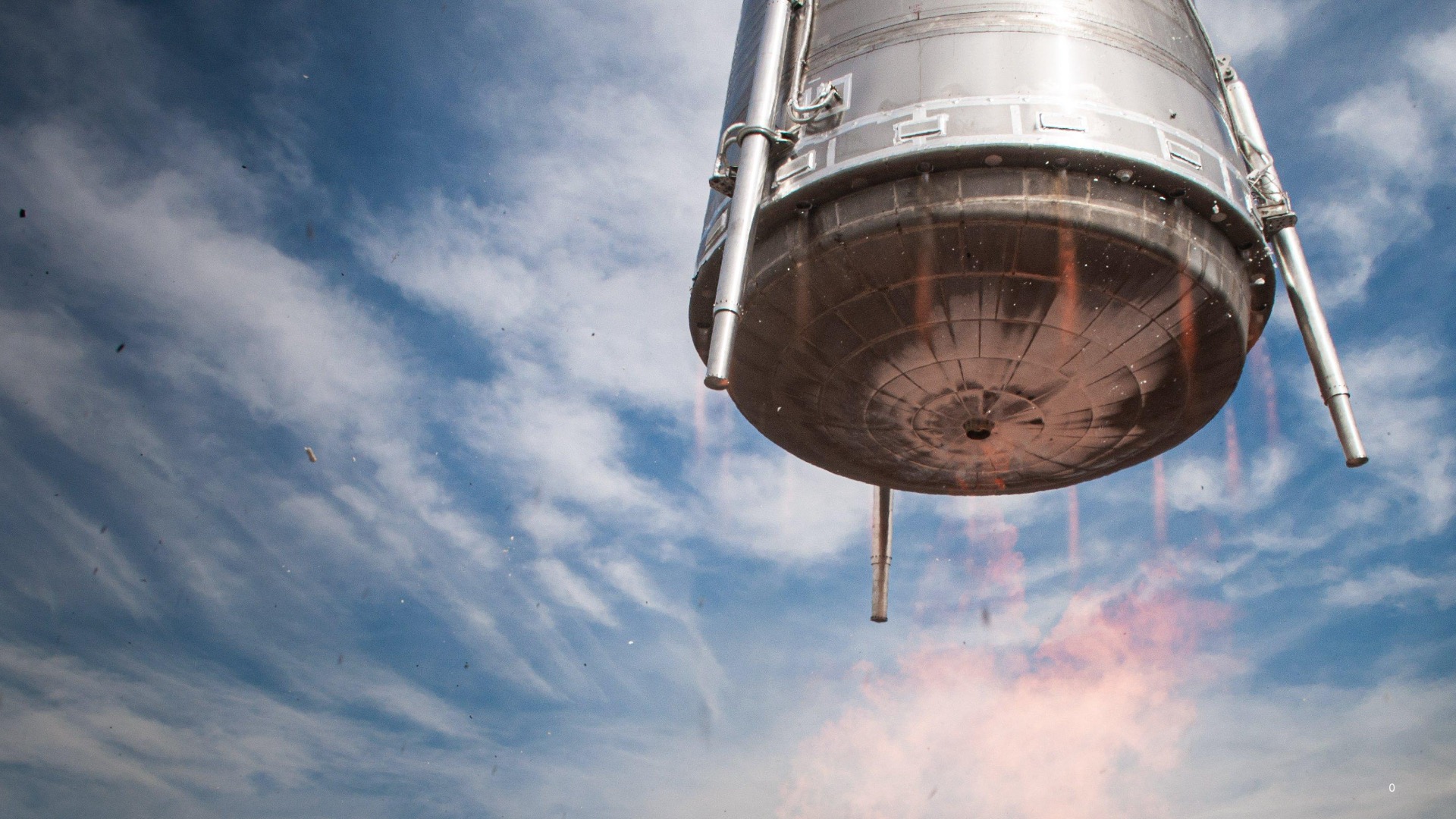
Building Rockets to Fly and Fly Again
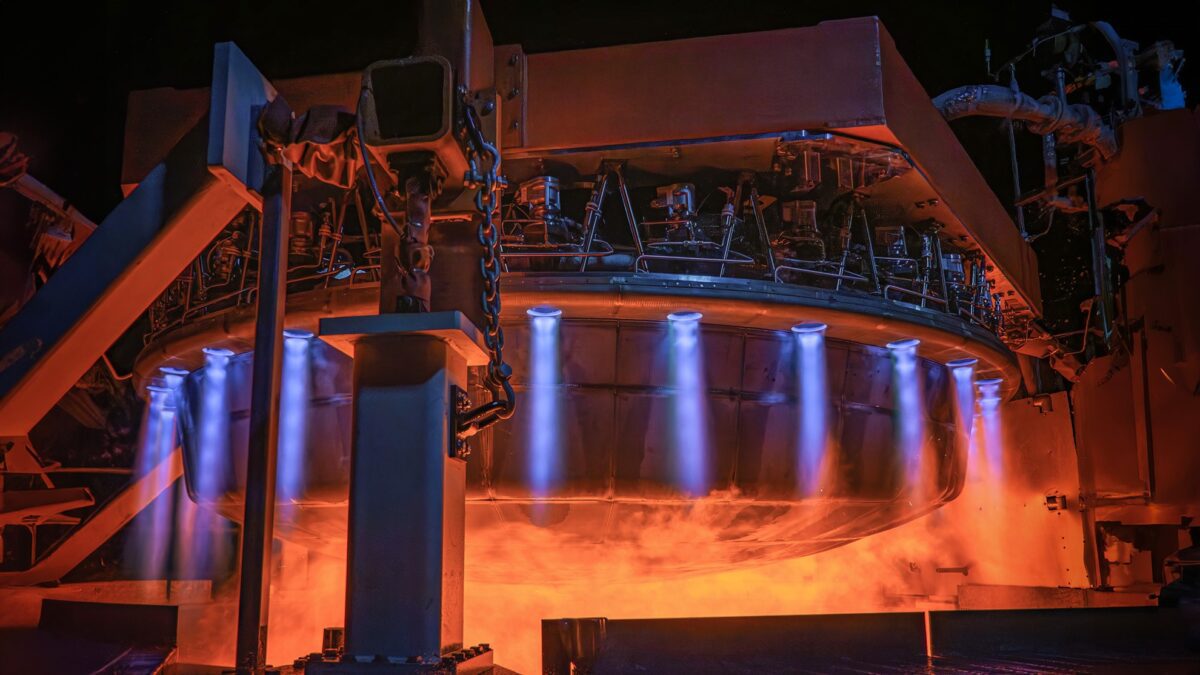
Why We Created the World’s First Bulletproof Heat Shield
At Stoke Space, we’re working on something that could change the way rockets—and access to space—work forever. It’s no secret that making rockets reusable is one of the biggest challenges in aerospace and only a few companies in the industry are focused on changing the game. While the idea of landing a rocket and flying it again sounds simple, the reality is far more complicated, especially when it comes to the second stage. This is the part of the rocket that goes all the way to space—and the part that’s usually just thrown away. Until now.
Second-stage reusability is the key to unlocking the potential of the future space economy. What’s one of the hardest problems to solve? Surviving the fiery journey back to Earth and keeping the second stage rapidly reusable. That’s where our heat shield comes in.
What Makes a Heat Shield So Important
Think of a rocket reentering the atmosphere like a car speeding downhill. The faster it goes, the more heat builds up to slow it down. Pushing on the brakes hard to slow it down causes the brakes and tires to heat up and continue getting hotter and hotter. This is similar to what happens to a second stage upon re-entry; without some level of overheating protection, the rocket would melt and break apart before it ever had a chance to land and be reused.
Most rockets today use heat shields made from ceramic tiles or materials that burn away during reentry. It works, but these solutions are fragile, expensive, and time-consuming to replace. This causes massive delays in refurbishment and reuse, and even then presents a reliability challenge. Imagine a car that needed all new tires and brake pads every time you drove it downhill. It’s doable, but it’s not ideal.
We knew there had to be a better way. So instead of sticking with traditional designs, we rethought the heat shield from the ground up.
A Heat Shield Built to Last
Our approach is different. We’ve designed a metal heat shield that’s not only incredibly tough but also built to be used again and again. Instead of breaking apart or wearing out, it stands up to the heat and stress of reentry and comes back ready for its next flight.
But we didn’t stop there. We combined the heat shield with the rocket’s engine, creating a single system that works together to protect the rocket and provide propulsion. Imagine a car where the engine cools the brakes while driving downhill—it’s that kind of integrated thinking that sets our design apart.
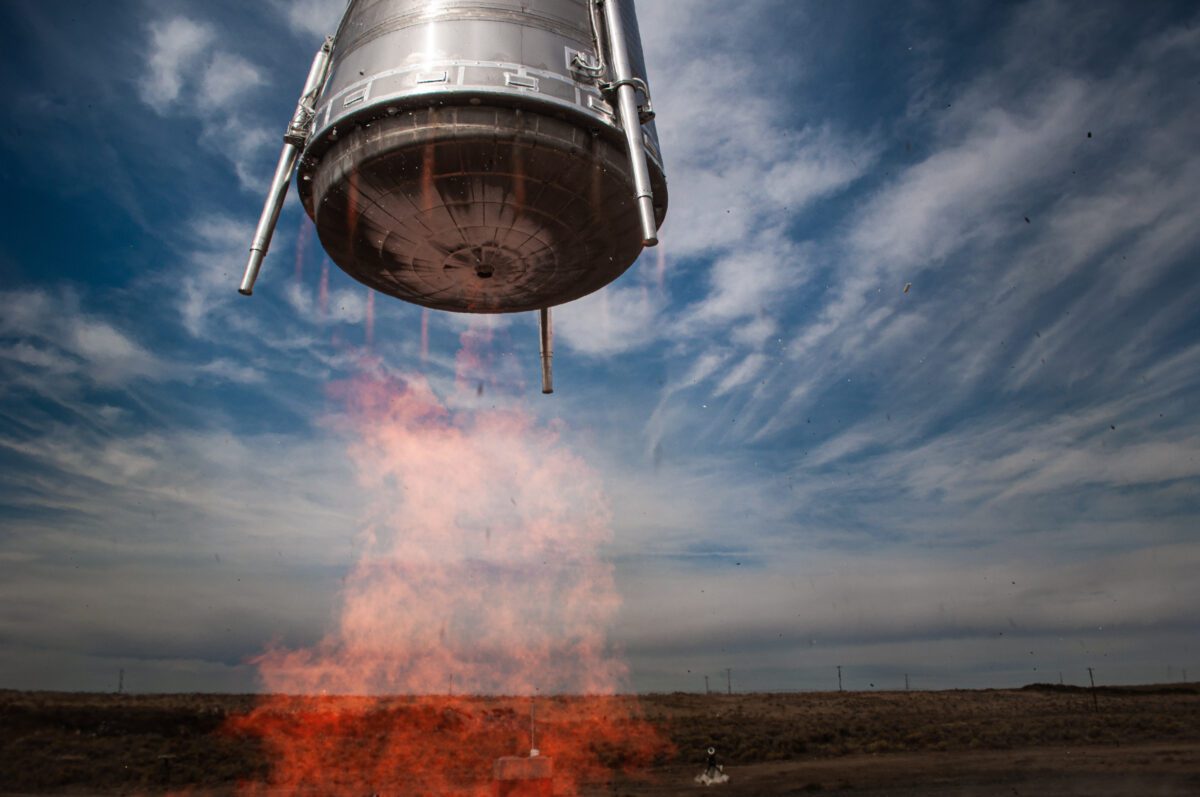
Staying Cool Under Pressure
What makes our heat shield special is how it handles heat. During reentry, we run liquid hydrogen through the shield, cooling it from the inside out using the same tanks and fluid flows that already exist to fuel the engine.
Why hydrogen? Two Words: Heat Capacity. Hydrogen is an excellent coolant because of its high specific heat capacity, which is the amount of heat energy required to raise the temperature of a substance. Liquid hydrogen, at an ultra-cold temperature of -423°F (-253°C), is perfect for both cooling and fueling. It absorbs the intense heat of reentry, protecting the heat shield, while its lightweight, high-energy fuel efficiently powers the rocket. Using hydrogen for both purposes simplifies the system, reduces weight, and maximizes performance and reusability.
Here’s a simple way to think about it: Imagine you’re cleaning up a spill with a sponge. A regular sponge might soak up some liquid, but it quickly gets saturated, leaving a mess behind. Now, picture a “super sponge” so advanced that it can hold an enormous amount of liquid without dripping or becoming full—this is like what hydrogen does with heat.
Hydrogen, especially in its supercritical state, has an incredibly high specific heat capacity. This means it can soak up large amounts of heat energy without its temperature rising dramatically. In technical terms, it’s exceptionally good at absorbing thermal energy and carrying it away to prevent overheating, much like that “super sponge” would handle spills effortlessly.
This matters most in situations where heat management is critical, such as during launch or re-entry. Supercritical hydrogen flows through cooling channels, “sucking up” the heat from the components, in this case the heat shield. Instead of burning up or overheating, the system stays stable because hydrogen efficiently moves that heat away.
Why Durability Matters
For us, this isn’t just about solving a tough engineering problem, it’s about changing what’s possible. A reusable rocket has to be tough, like a reliable truck that keeps running no matter the terrain. That’s the level of durability we’re aiming for.
Stoke Space’s heat shield is literally bulletproof, and that’s no exaggeration—it’s a durable metal design built to withstand the harshest conditions of spaceflight and reentry. Unlike fragile tiles or ablative coatings, our shield doesn’t chip, crack, or burn away. It was engineered with the founding thesis that a truly reusable rocket must be as tough as the challenges it faces. By integrating the heat shield with the engine and actively cooling it with liquid hydrogen, we’ve created a system that can not only survive the journey back to Earth but thrive, ready to fly again with minimal refurbishment.
Proven Technology
The concept of using hydrogen, or other fluids, to cool rocket components is not new; in fact, it’s been a cornerstone of rocket engineering for decades. Rocket fuel (and sometimes even the oxidizer) has long been used in dual capacity as a coolant to keep rocket thrust chambers and nozzles cool during operation. In these regeneratively cooled systems, the coolant absorbs the intense heat generated during combustion, preventing structural damage while simultaneously transitioning into a gaseous state for fuel.
By adapting this proven cooling method for our heat shield, we’re taking advantage of decades of reliable technology in a novel way. In addition to cooling engine parts, we’re extending this approach to protect the entire second stage during reentry. The physics are the same: the rocket fuel circulates through the heat shield, absorbing and dissipating the extreme heat of atmospheric reentry. Our choice of fuel, liquid hydrogen, is particularly good for this purpose since its cooling capacity is about five times better than any other fuel. This integration isn’t just innovative, it’s grounded in a foundation of tried-and-true engineering principles, giving us confidence in its effectiveness and reliability.

Humble Beginnings, with Bold Goals
We know this is a bold undertaking and know we’re not the first to try to make rockets reusable. Several companies have already shown it’s possible to recover and reuse the first stage, and SpaceX is making huge strides in this area with their Starship second stage and Super Heavy booster. Even before that, NASA’s Space Shuttle laid the groundwork for reusability. But “rapid” reuse of the second stage—the part that goes all the way to orbit and back—remains a challenge, and we are laser focused on the solution.
We’ve successfully tested our heat shield on our test stand in Moses Lake, WA, and it’s endured heat loads even higher than those expected during reentry. These ground tests proved the shield’s durability and cooling system under extreme conditions. That said, physics behave differently in flight, so the next critical step is to validate its performance during an actual reentry. Flying will provide the final proof that our design is ready for the demands of full reusability.
We believe that by solving the heat shield problem, we’re unlocking the potential for rockets that can be turned around quickly and affordably. It’s like moving from disposable cameras to smartphones. With reusability, space becomes more accessible and less wasteful, opening doors to more exploration, more science, and more opportunities.
Fly, and Fly AGAIN
At Stoke Space, we’ve started with the second stage because we believe solving this piece unlocks the future of 100% reusable rockets. Our work is still in progress, and we have a lot left to prove, but we’re confident in the path we’ve chosen.
Our goal isn’t just to make a rocket that flies. It’s to make a rocket that flies, lands, and flies again—over and over and over, the same way a 737 takes off, flies and lands then fuels up and flies again.
We’re excited to share this journey with you and grateful for the support and belief in what we’re building. Together, we’re taking a big step toward making spaceflight as routine as air travel.
Stay tuned. More to come.
